Die Stadt Salzgitter ist der drittgrößte Industriestandort Niedersachsens. Die Frage „Wofür ist Salzgitter bekannt“ wird Google sehr häufig gestellt und ich war entsprechend neugierig auf die Antwort. Sie können sich meine Enttäuschung vielleicht vorstellen, als ich bemerke, dass die Suchmaschine keine Antwort liefert. Da hilft nur eins: Ich muss nach Salzgitter fahren, um herauszufinden, wofür Salzgitter bekannt ist.
Spezial: Blick hinter die Kulissen Salzgitters
– Drei Werksbesichtigungen
Der Umstand, dass viele in Salzgitter ansässige Unternehmen Besucher einladen, einen Blick hinter die Kulissen zu werfen, erleichtert meine Recherche. Meine erste Station ist die wohl spektakulärste: Ich habe eine Werksführung bei der Salzgitter AG gebucht.
Vom Erz zum Stahl: Besuch bei Salzgitter Flachstahl
Als ich morgens um 8 Uhr das Besucherzentrum der Salzgitter AG betrete, bin ich noch skeptisch: Werde ich tatsächlich Ströme flüssigen Roheisens sehen? Werde ich den Weg vom Eisenerz zu Stahlblechrollen, sogenannten Coils, verfolgen können?
Bevor alle Besucher mit Helmen, Schutzbrillen, Kopfhörern und besonderen Sichtblenden ausgestattet werden, sehen wir ein Video, das alle Produktionsprozesse und -schritte bei Salzgitter Flachstahl erklärt.
Mit dem Bus geht es anschließend zu einem von mehreren Hochöfen. Wir haben Glück. Vor kurzem ist der Abstich erfolgt. Durch die Sichtblenden können wir beobachten, wie das flüssige Roheisen in die bereitstehenden Torpedopfannenwagen fließt. Obwohl das Roheisen eine Temperatur von etwa 1450 Grad Celsius hat, komme ich hier nicht ins Schwitzen.
Unsere Besuchergruppe folgt dem Weg des flüssigen Roheisens ins eigentliche Stahlwerk. In dieser gigantischen Halle entsteht in drei LD-Konvertern aus Roheisen Rohstahl. Unter Beachtung sämtlicher Sicherheitsvorschriften verlassen wir das Stahlwerk und steuern das Warmwalzwerk an.
Dem Rohstahl werden zwischenzeitlich Legierungselemente zugesetzt. So erhält der Stahl die vom Kunden gewünschten individuellen Qualitäten. Dann werden die Stahlsorten in Stranggießanlagen zu Brammen vergossen. Bis zu 35 Zentimeter dick und bis zu 32 Tonnen schwer sind die Brammen. Der Großteil des Stahls ist unter einer erstarrten Schale noch flüssig.
Im Warmwalzwerk begegnen wir den Brammen wieder. Und hier ist es auch endlich so kuschelig warm, wie ich es erwartet habe. Denn die Brammen werden hier in Wärmeöfen auf etwa 1250 Grad erhitzt und zu Warmbreitband gewalzt. Dies ist ein ebenso beeindruckender Vorgang wie die Herstellung von Roheisen und Stahl. Das entstehende Band hat je nach Dicke eine Länge von bis zu 2000 Metern. Am Ende der Walzstraße wird das Band zu einem Coil aufgewickelt.
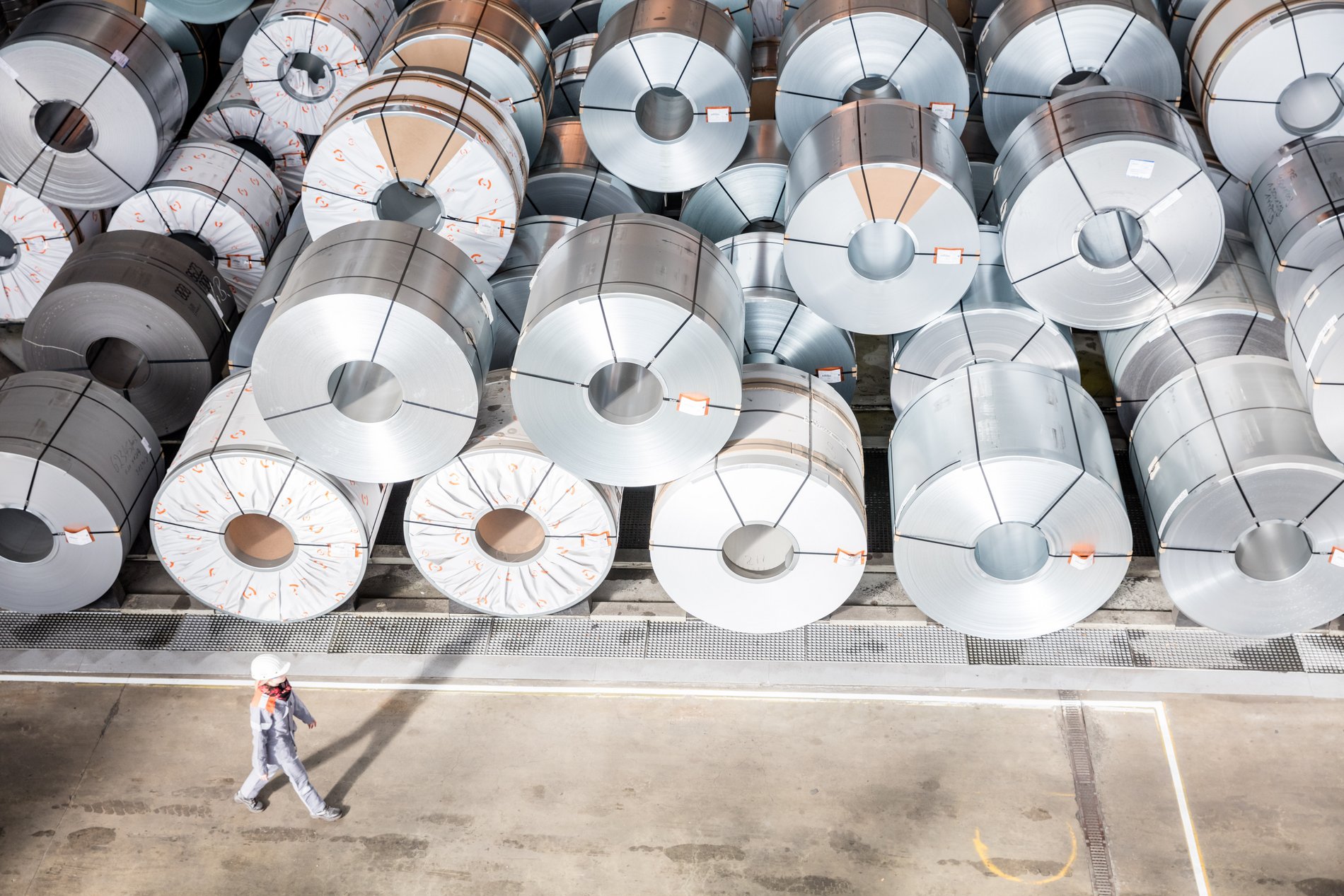
Zurück bei meinem Auto, das aus Salzgitter-Stahl besteht, bin ich mir sicher: Salzgitter ist weltweit für Stahl bekannt. Doch vor mir liegen zwei weitere Werksführungen. Als nächstes bin ich beim Volkswagenwerk Salzgitter angemeldet.
Vom Bugatti- bis zum ID-Motor: Besuch bei Volkswagen Salzgitter
Nein, Autos werden im Volkswagenwerk in Salzgitter schon lange nicht mehr gebaut. Obwohl das ganze Werk ursprünglich für den Bau von Fahrzeugen ausgelegt war. So wurden hier in den Jahren 1970 bis 1975 der bei NSU entwickelte VW K 70, die VW-Modelle 411 und 412 sowie der Passat gefertigt.
Heute ist Salzgitter das Motorenleitwerk des Volkswagenkonzerns. Motorenleitwerk heißt, dass die Richtlinien für alle anderen Motorenwerke des Konzerns aus Salzgitter kommen. Mehr als 200 verschiedene Motorvarianten können hier produziert werden. Damit ist Salzgitter eines der vielfältigsten Komponentenwerke des Konzerns weltweit.
Die Palette reicht von Benzin- über Diesel- bis hin zu Hybridmotoren und vom 3-Zylinder bis zum 16-Zylinder. Zwischenzeitlich wurden hier auch Industriemotoren, Bootsmotoren und sogar Blockheizkraftwerke gefertigt. Jetzt erweitern auch Statoren und Rotoren für den E-Motor die Produktvielfalt des Werkes.
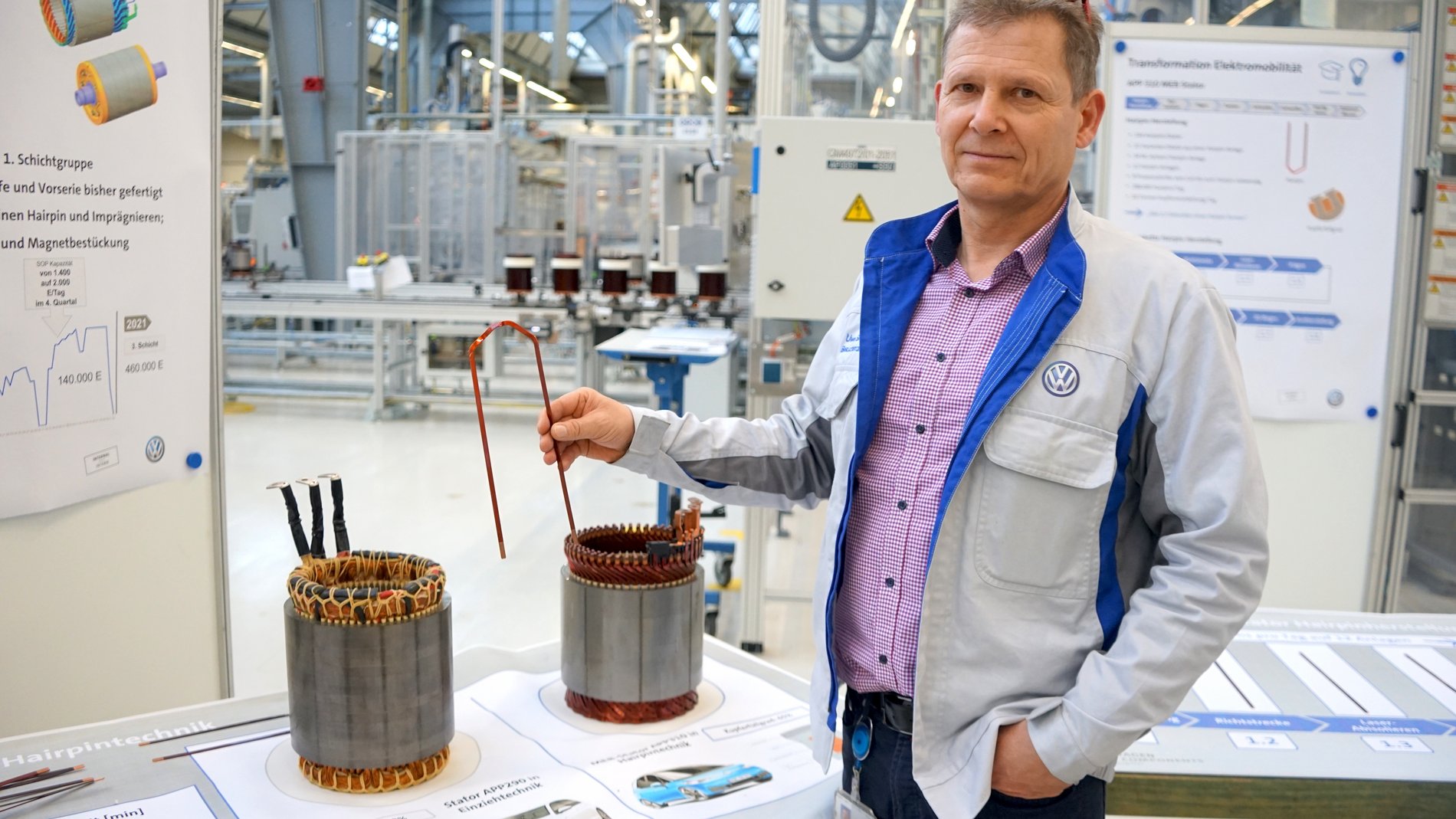
Uwe Stiebeling vom Volkswagen-Besucherdienst hat mich in seinen E-Golf eingeladen und braust mit mir emissionsfrei durch die Hallen. Gruppen bis 18 Personen kann der Besucherdienst in einem besonderen Fahrzeug transportieren, doch auch Fußtouren durch das Werk sind möglich.
Teilnehmer an Walking Tours sollten allerdings auf gutes Schuhwerk achten. 2,8 Quadratkilometer umfasst das Werksgelände, der Standort beschäftigt rund 7000 Mitarbeiter. Dazu zählen 500 hochqualifizierte Kollegen für den Bereich E-Mobilität. Insgesamt können in Salzgitter täglich bis zu 7000 Motoren gebaut werden, etwa 4000 davon sind Otto-Motoren. Hinzu kommen schon bald bis zu 2000 Statoren und Rotoren täglich.
Unser erster Stopp ist die Endmontagelinie für den Motor EA211evo mit 1,5 Litern Hubraum und vier Zylindern. Hier sehe ich eine produktionstechnische Revolution: Ein Mann und zwei Roboter stehen einträchtig nebeneinander und montieren Ölkühler, Ölabscheider und Dichtungen. Dieses Arbeiten ohne Schutzzäune ist möglich, seit Roboter dank Sensoren erkennen können, wenn etwas in ihr Aktionsfeld kommt. In diesem Fall bleiben sie sofort stehen.
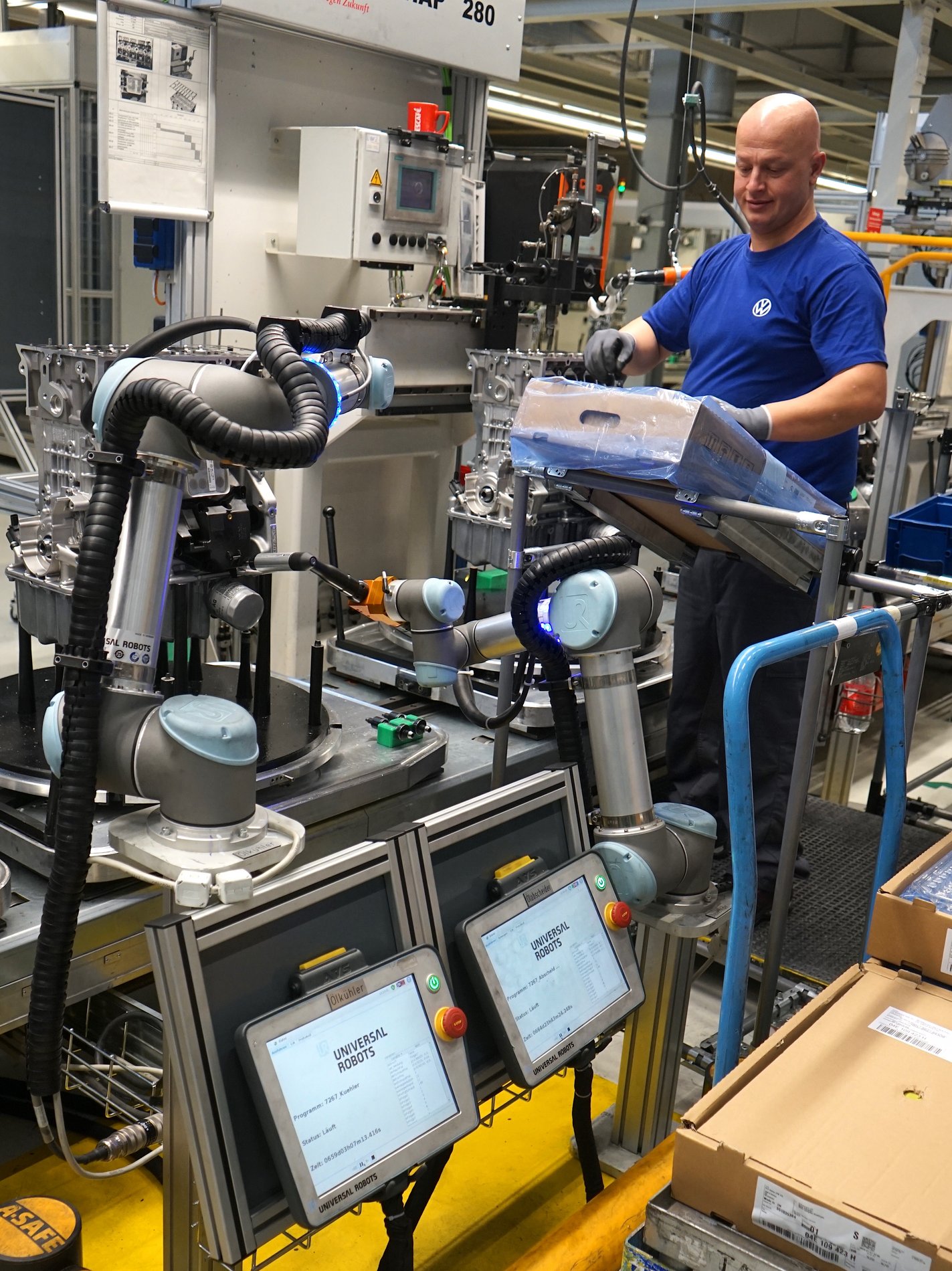
„Das ist erst der erste Schritt“, erklärt Uwe Stiebeling. Künftig werden sich kooperierende Roboter und Menschen beispielsweise Gegenstände anreichen können. Für die Mitarbeiter stellen die neuen, elektronischen Kollegen eine Arbeitserleichterung dar.
Apropos Arbeitserleichterung: Jetzt halten wir an einer vollergonomisch gestalteten Fertigungslinie an. Hier findet jeder Mitarbeiter – egal, ob eher klein oder hoch gewachsen – den zu montierenden Motor in der für ihn optimalen Arbeitshöhe und Position vor. Zudem gibt es Arbeitsplätze, an denen die Mitarbeiter auch sitzen können. Mit dieser Errungenschaft wird Volkswagen dem steigenden Altersdurchschnitt der Produktionsmitarbeiter gerecht.
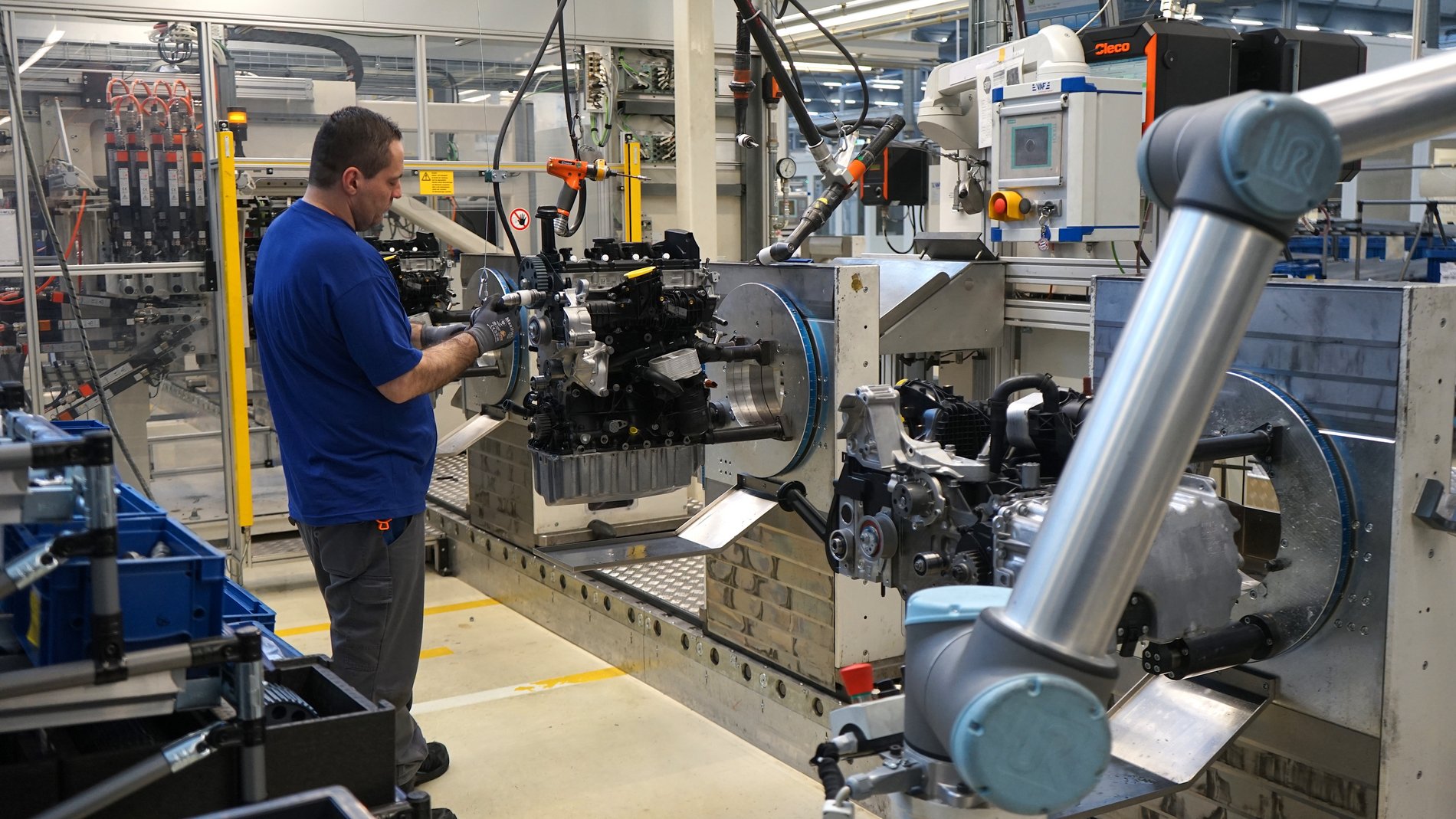
Nun kommen wir zur Fertigung von Stator und Rotor. Das sind zwei Bauteile des neuen Grundelektromotors, der alle Modelle der vollelektrischen ID-Familie antreiben wird. Roboter sind hier damit beschäftigt, sogenannte Hairpins zu einem Herzstück des Motors, dem Stator, zusammenzusetzen und zu verlöten. Zuvor formt eine vollautomatische Anlage täglich rund 300.000 Haarnadel-artige Kupferteile aus Rollenware.
Uwe Stiebeling verdeutlicht die Dimensionen der Anlage, die seit einigen Wochen läuft: „Die Stückzahl ist weltweit einmalig. Wir fertigen hier täglich Statoren und Rotoren für künftig bis zu 2000 Elektromotoren. Zum Vergleich: Tesla plant, pro Woche 3000 Autos zu bauen.“
Zufällig treffen wir hier Jens Falkenberg, den Abteilungsleiter Elektroantriebe. Er nimmt sich die Zeit, mir einige erstaunliche Fakten über die MEB-Plattform (MEB heißt Modularer Elektrobaukasten) mitzuteilen. So verfügen Fahrzeuge, die auf der MEB-Plattform basieren – mit Ausnahme der allradangetriebenen SUV – über Heckantrieb. Das Getriebe hat keinen Rückwärtsgang, vielmehr dreht sich der Motor zum Rückwärtsfahren rückwärts. Und auf Außenspiegel hat man zugunsten des cw-Werts verzichtet. (Anmerkung: cw-Wert ist ein dimensionsloses Maß für den Strömungswiderstand eines von einem Fluid umströmten Körpers. Umgangssprachlich ausgedrückt ist der -Wert ein Maß für die „Windschlüpfigkeit“ eines Körpers, Quelle Wikipedia.)
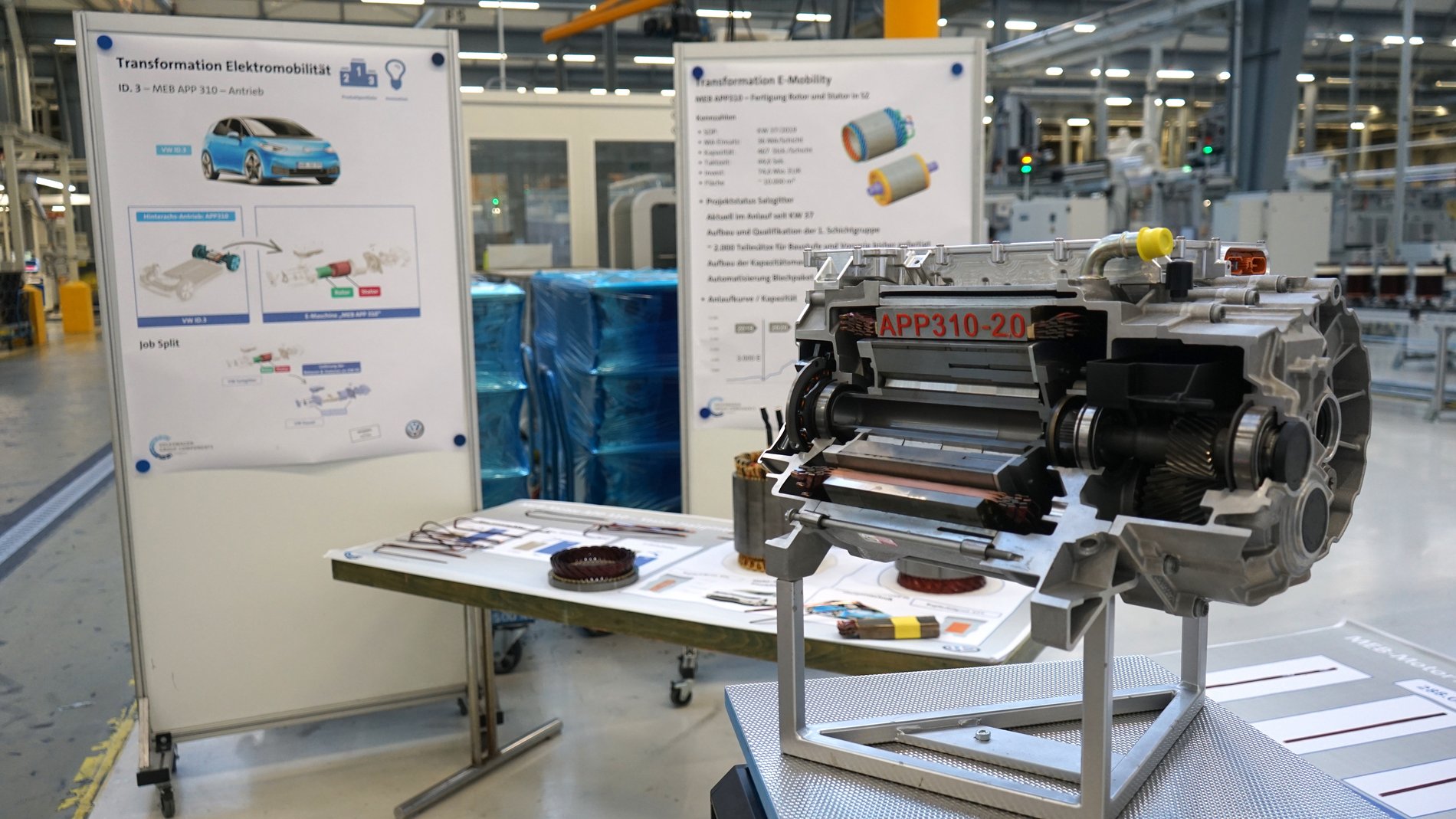
Wo wir gerade über Elektromobilität sprechen: Im VW-Werk Salzgitter ist auch das neu gegründete Geschäftsfeld Batteriezelle angesiedelt. Im entsprechenden Center of Excellence beschäftigen sich die Mitarbeiter mit der Entwicklung und der Fertigungsentwicklung von Batteriezellen. Damit nicht genug, denn: „In einem Joint Venture mit dem schwedischen Unternehmen Northvolt wollen wir hier ab 2024 eigene Batteriezellen in Großserie fertigen“, sagt Uwe Stiebeling.
„Wir können alles: Otto und Diesel, kompakt und Bugatti, E-Antrieb und Batteriezellen“
Für den Schluss hat Uwe Stiebeling ein weiteres Highlight aufgespart: die Fertigung des Bugatti-Chiron-Aggregats. In der hochgeheimen Pilothalle Aggregate widmet sich ein eigener kleiner Ausstellungsraum diesem Wunderwerk der Technik. Und hier wird auch der Chiron-Motor in reiner Handarbeit hergestellt. Das hochspezialisierte kleine Team schafft zusammen etwa 100 Stück pro Jahr.
Der Chiron ist Welten von anderen Sportwagen dieser Welt entfernt und sein Herzstück ist der schnellste Serienmotor der Welt: der V16-Motor mit 1500 PS. Erst unlängst hat der Chiron wieder einen Geschwindigkeitsrekord gebrochen und ist jetzt das erste Serienfahrzeug, das 490 Stundenkilometer schnell gefahren ist.
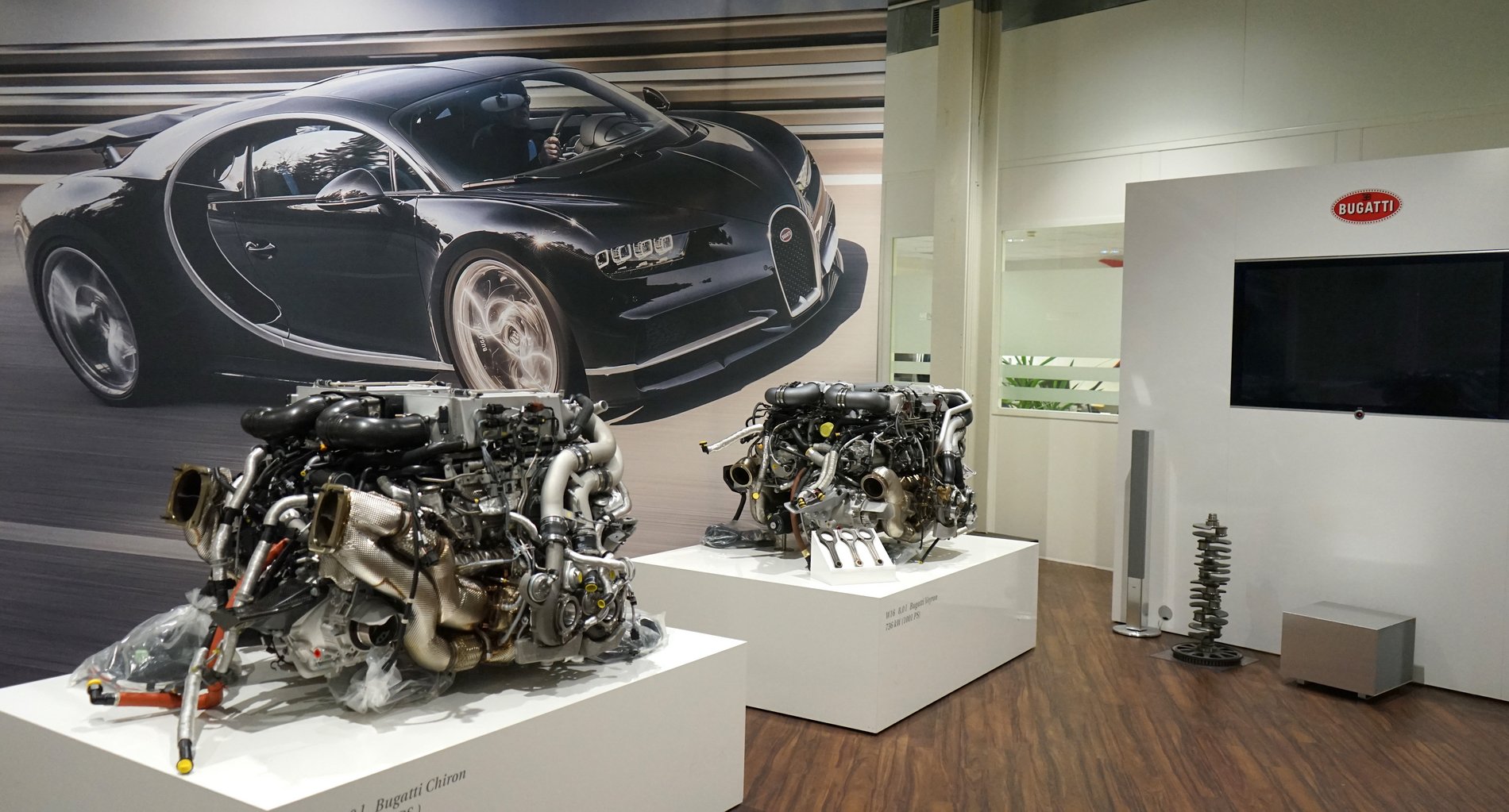
Mit schlafwandlerischer Sicherheit errät Uwe Stiebeling mein Traummodell unter den neueren Bugattis – den Roadster Veyron 16.4 Grand Sport Vitesse. Wir schauen ein Video mit fahrenden Bugattis an, ich träume ein bisschen davon, einmal in diesem Wagen zu fahren und mir das Haar zausen zu lassen.
Doch Uwe Stiebeling kennt kein Pardon. Ein paar Minuten später setzt er mich bei meinem betagten Modell eines Mitbewerbers ab – ich bin wieder in der Realität und nehme mir vor: Mein nächstes Auto ist wieder ein Konzernfahrzeug.
Und ich überlege, ob Salzgitter nicht etwa für die Motoren, die hier hergestellt werden, bekannt ist? Kein Ding der Unmöglichkeit, schließlich treiben Motoren aus Salzgitter weltweit Autos an. Doch meine Rundreise durch Salzgitters Wirtschaftswelt ist noch nicht zu Ende.
Ortwechsel: Wilhelm Fromme Landhandel, Verladestation am Beddinger Hafen
In Salzgitter-Beddingen erkunde ich nun einen ganz anderen Wirtschaftszweig. Vom am Salzgitterstichkanal gelegenen Hafen gelangt hochwertiges Getreide beispielsweise in die arabischen Emirate. Wieso man im Nahen Osten Nahrungsmittel aus der Salzgitter-Region zu schätzen weiß, erfahre ich von Kurt Fromme, dem Geschäftsführer der Wilhelm Fromme Landhandel GmbH & Co.KG.
An einem der wenigen Morgen mit Frost in diesem Winter bin ich auf dem Weg nach Beddingen. Die Sonne erhebt sich über leichtem Bodennebel und Raureif – ein traumhaft schönes Bild. Zwischen den Getreidesilos am Hafen und dem kleinen Betriebsgebäude des Unternehmens herrscht scheinbar Ruhe.
Doch ich habe die Eingangstüre noch nicht erreicht, als Bewegung in die Szenerie kommt: Ein Lastwagen fährt vor und stoppt neben dem unscheinbaren Gebäude auf der LKW-Waage. Er liefert Getreide an. Während der Fahrer mit den Papieren ins Büro geht, bewegt sich wie von Geisterhand ein Rüssel über den geöffneten Frachtraum. Mehrmals taucht der Schlauch an unterschiedlichen Stellen in die Ladung und saugt Proben an.
Zu meiner Überraschung landen die Proben direkt neben dem Büro in einem Labor. Hier wartet Karin Ehlers schon auf die Getreidekörner, um sie einer eingehenden Analyse zu unterziehen. Unter den wachen Augen eines Mitarbeiters der Lebensmittelaufsichtsbehörde nimmt sie eine sensorische Prüfung vor. Will heißen, sie begutachtet Aussehen und Geruch des Getreides.
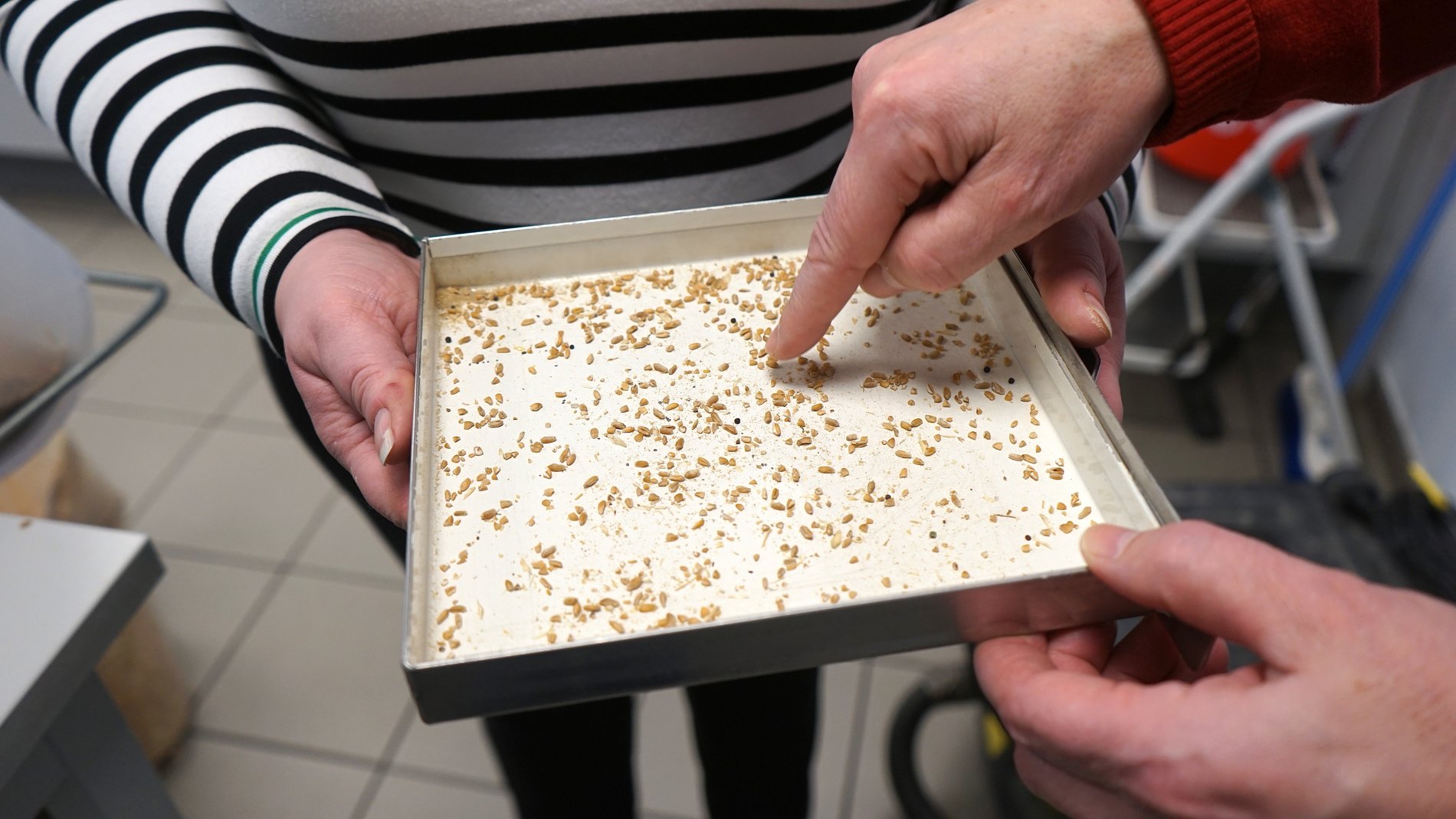
Wenn die erfahrene LTA (Landwirtschaftlich-technische Assistentin) damit zufrieden ist und weder Tiere noch andere Fremdkörper sichtbar sind, stehen weitere Untersuchungen an: Feuchtigkeits- und Proteingehalt werden festgestellt, die Qualität des Proteins, Enzymaktivität und Gewicht.
Kurt Fromme hat mich ins Labor begleitet und erklärt mir jetzt, warum Karin Ehlers zusätzlich Spezialuntersuchungen des angelieferten Getreides vornimmt. „Für Getreide gibt es keine wissenschaftliche Forschung mehr. Da Qualität für uns höchste Priorität hat, haben wir eigene Analysemethoden entwickelt.“
So wird beispielsweise der mikrobakteriologische Zustand des Getreides anhand eines Messgerätes festgestellt, das Wilhelm Fromme Landhandel gemeinsam mit dem Max-Rubner-Institut in Detmold entwickelt hat.
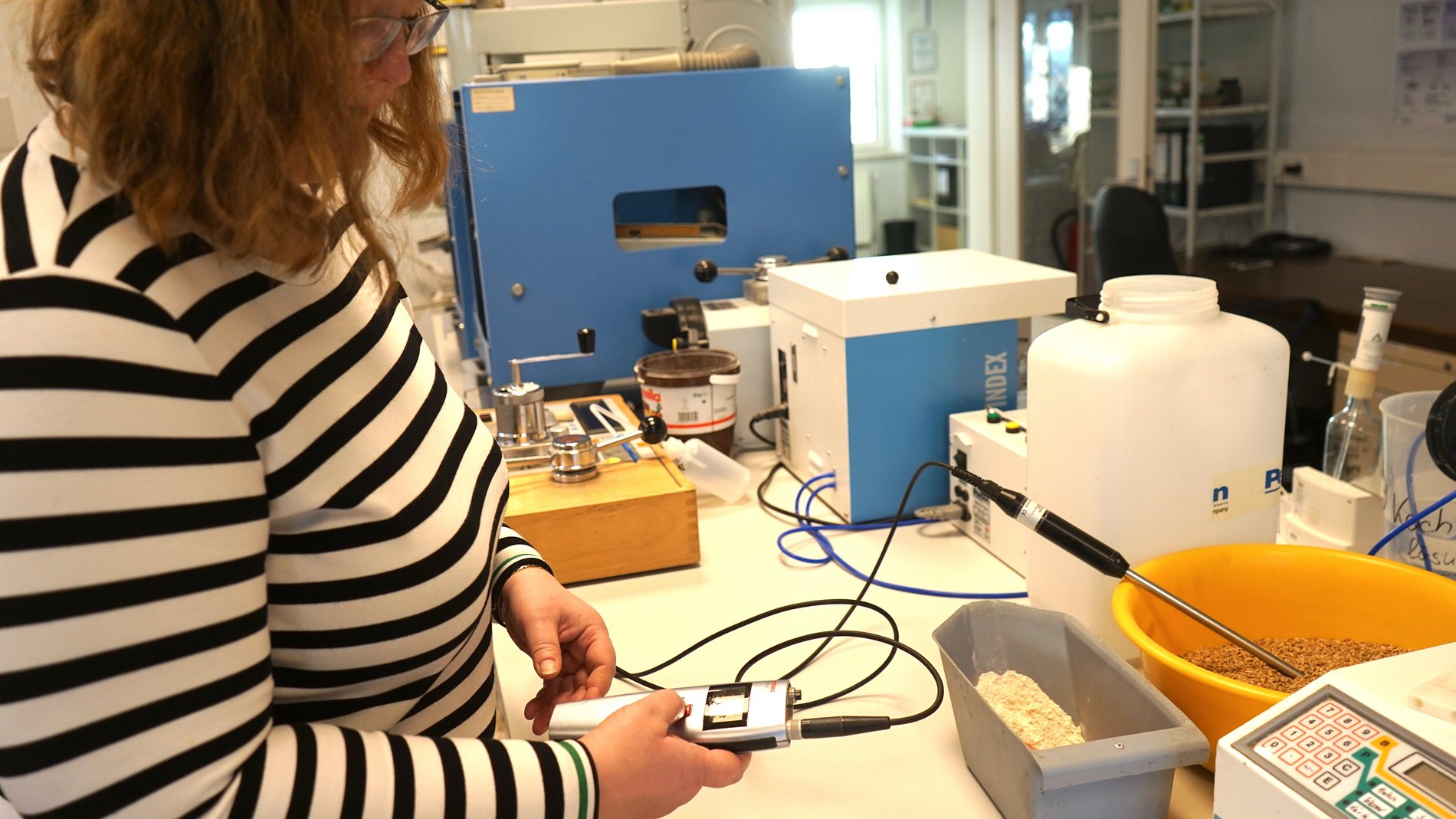
Neben dem Labor befindet sich eine kleine Versuchsbäckerei, die manchmal auch in Betrieb genommen wird, wenn Besuchergruppen angemeldet sind. „Die meisten Besucher sind begeistert von unserem Brot“, schmunzelt Kurt Fromme.
Ich verstehe allerdings immer noch nicht, warum das Unternehmen hier in der Landhandel-Verladestation zwischen Silos, Förderbändern und Kanalufer so viel Aufwand betreibt, um Getreide zu analysieren. „Wir homogenisieren das Getreide auch. Das heißt, wir mischen beispielsweise unterschiedliche Weizensorten, um Zusatznutzen aus den einzelnen Sorten herauszuholen. Deshalb müssen wir die Eigenschaften kennen und auch ausprobieren, wie sich die Mischungen backen“, erklärt Kurt Fromme.
Als Landhandel geht er auf die Mühlen und im internationalen Geschäft auf Großhändler – also seine Kunden – zu und bietet die entwickelten Getreidemischungen an. Dass Fromme für die qualitativ hochwertigen Mischungen einen entsprechenden Preis verlangen kann, versteht sich.
Die Kunden des Unternehmens befinden sich in Deutschland, im europäischen Binnenland und beispielsweise im Nahen Osten. „Für Kunden in islamischen Staaten ist die Reinheit des Getreides sehr wichtig, nicht nur hinsichtlich der Inhaltsstoffe, sondern auch optisch. Da sie aus politischen Gründen nicht in den USA kaufen, kommen sie gerne zu uns“, so Fromme.
Das Unternehmen legt in allen betrieblichen Abläufen größten Wert auf Lebensmittelsicherheit. „Verbraucherschutz wiegt höher als Betriebswirtschaft“, sagt Kurt Fromme. Er will, dass der Kunde zurückkommt, nicht die Ware. Das gelingt fast immer. „Wir haben eine Reklamationsquote von 0,02 Prozent. In unserer Branche sind 1,5 bis 2 Prozent üblich.“
Für absolute Sicherheit hat die Wilhelm Fromme Landhandel GmbH & Co.KG 10 Millionen Euro in den Standort Beddingen investiert. Die Verladestation hat eine Annahmeleistung von beachtlichen 500 Tonnen Getreide pro Stunde. Dementsprechend beträgt die Verladeleistung auf die Schiffe ebenfalls 500 Tonnen pro Stunde. Zwischen Annahme und Verladung durchläuft das Getreide unter Anderem komplexe Reinigungssysteme. „Am Ende bleiben 70 Prozent des angelieferten Rohstoffs übrig“, so Fromme.
Ich erfahre noch, dass Getreide 70 Prozent der angekauften und verkauften Produkte beziehungsweise Rohstoffe ausmacht. Die restlichen 30 Prozent verteilen sich auf Düngemittel und Ölsaaten. Und ich lerne, dass die Besucher der Verladestation mehr über Lebensmittel erfahren wollen.
Mit einer Besichtigung der halbautomatischen elektronischen Verladung des Getreides aufs Schiff endet meine Werkstour. Hier hat Silomeister David Mahn, der gelernter Bäckermeister ist, die Übersicht über den Verladevorgang. Das Maschinenhaus dürfen Besucher aus hygienischen Gründen nicht betreten. Und den Spaziergang zum Kanal, wo das Schiff liegt, das beladen wird, schenke ich mir. Denn inzwischen haben sich Wolken vor die Sonne geschoben und es pfeift ein eisiger Wind.
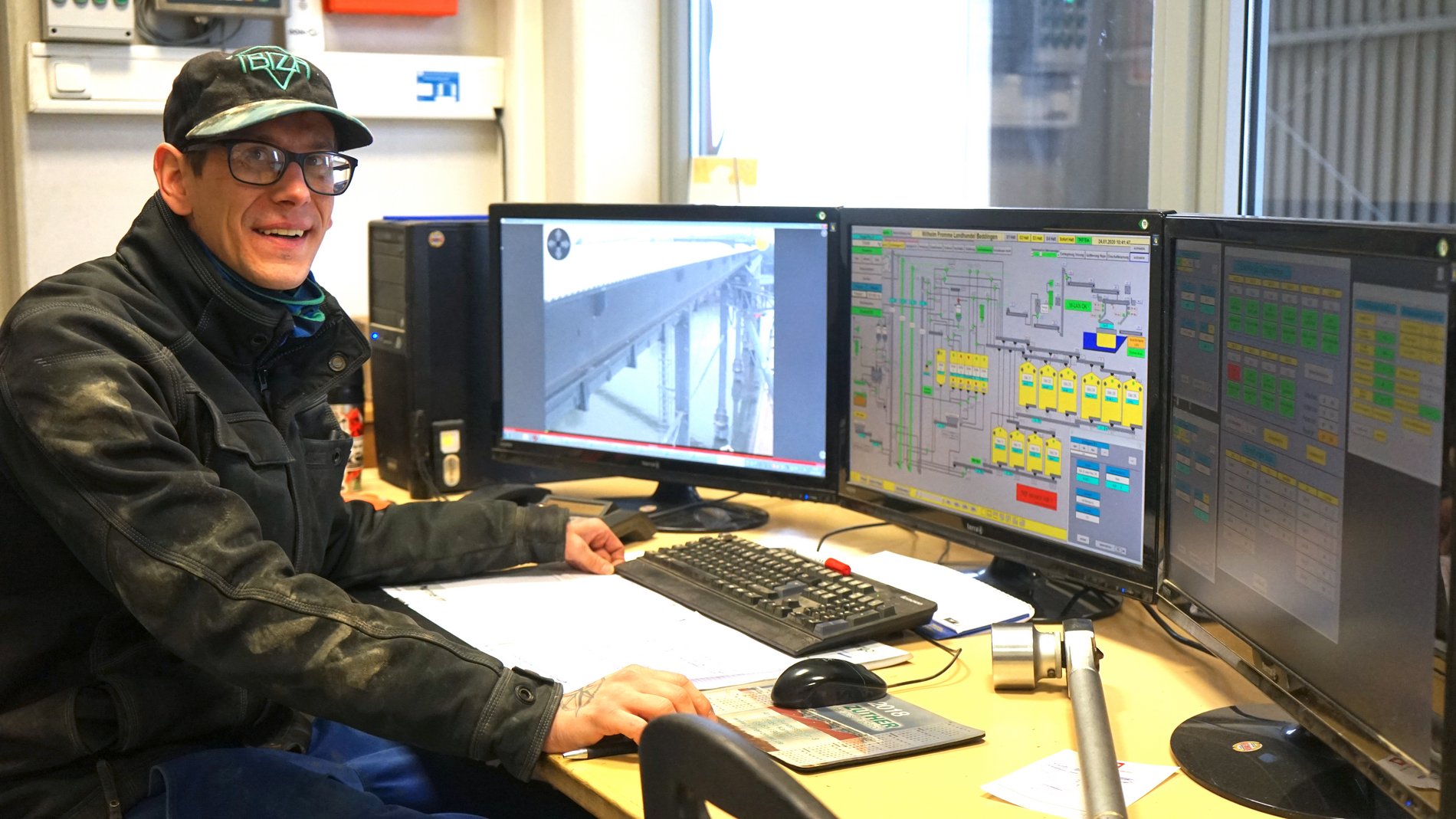
Ich verabschiede mich von Kurt Fromme und überlege, ob Salzgitter möglicherweise für qualitativ hochwertiges Getreide bekannt ist, das von hier aus in die Welt geht. Jedenfalls kann ich Googles Problem jetzt nachvollziehen. Alle Unternehmen, die ich in Salzgitter besichtigt habe, leisten einzigartige Arbeit. Und nicht nur sie. In Salzgitter gibt es noch viel mehr zu sehen. Möge sich jeder selbst ein Bild machen und am Ende eine Meinung bilden, wofür Salzgitter wohl bekannt sein könnte.
Anmeldung zur Hüttenwerksbesichtigung: Einzelpersonen (Mindestalter 16 Jahre) können sich direkt bei der Tourist-Information anzumelden. Tel. 05341-9009940 oder info@tourismus-salzgitter.de
Anmeldung zur Besichtigung des Volkswagenwerks Salzgitter: Der Volkswagen-Besucherdienst nimmt Anmeldungen telefonisch unter Tel. 05341-232236 entgegen. Das Mindestalter beträgt zehn Jahre. Werkstouren dauern etwa zwei Stunden und finden montags bis freitags um 10.00 Uhr und um 14.00 Uhr statt.
Anmeldung zur Besichtigung der Verladestation Beddingen: Bitte nehmen Sie Kontakt auf zur Wilhelm Fromme Landhandel GmbH & Co.KG, Telefon 05341-867280,
E-Mail info@wilhelmfromme.de
Viele weitere Werksführungen und Betriebsbesichtigungen finden Sie in der aktuellen zeitORTE-Broschüre. Gibt es hier zum Download.
Dieser Beitrag wurde für den Blog der zeitORTE verfasst von Beate Ziehres