Immer leichter, immer fester, immer besser zu verformen: Beim Thema Stahl ist noch einiges möglich. Schließlich ist Stahl einer der ältesten und gängigsten Werkstoffe der Menschheit. Und das wird auch so bleiben, obwohl viele Experten den Werkstoff schon zum Auslaufmodell erklärt haben.
Rezepte aus der Stahlküche
Wie die Salzgitter AG innovative Stähle entwickelt
Stahl wieder im Trend
„Stahl hat Zukunft, der Trend weg vom Stahl beim Autobau ist seit zwei Jahren gestoppt. Es ist der richtige Werkstoff an der richtigen Stelle“, sagt Dr. Frank Klose, der bei der Salzgitter Mannesmann Forschung (SZMF) den Bereich Werkstoff- und Prozessentwicklung leitet. Das Unternehmen ist die zentrale Forschungsgesellschaft der Salzgitter AG. An den beiden Standorten Salzgitter und Duisburg erforschen rund 300 Mitarbeiter die Zukunft des universellen Werkstoffs Stahl.
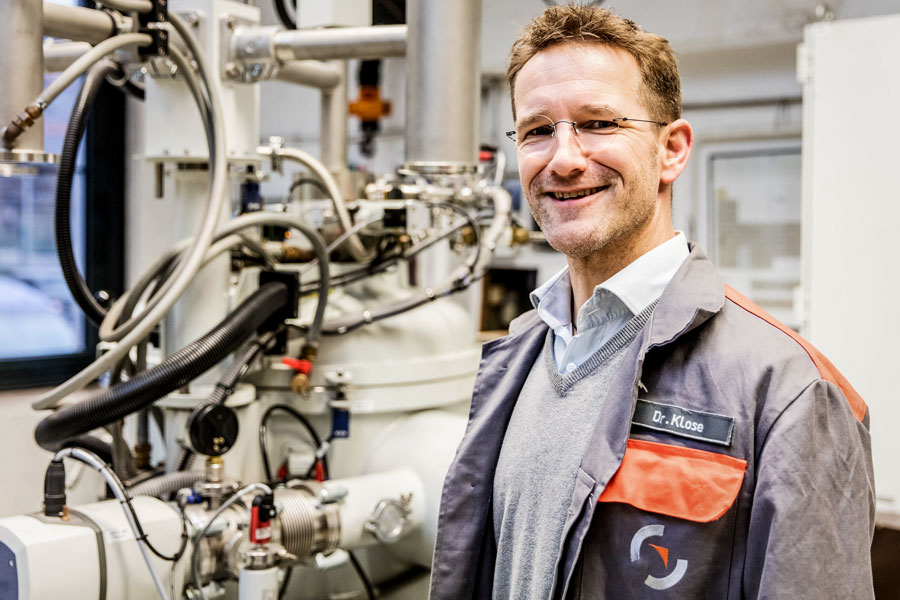
Ein wichtiger Bereich ist die Entwicklung neuer Stahlsorten, Oberflächen und Anwendungen für den Fahrzeugbau. Schließlich muss gerade die Autoindustrie unter dem Druck gesetzlicher Vorgaben stärker auf Nachhaltigkeit und Ressourceneffizienz setzen und zugleich die Kosten im Griff behalten. „Hier hat der Stahl zwei unschlagbare Vorteile“, sagt Klose. Zum einen sei die Energiebilanz für den gesamten Lebenszyklus deutlich besser als bei anderen Werkstoffen, zum anderen das Zusammenspiel von Gewicht, Festigkeit, Verarbeitbarkeit, Preis und Energiebilanz besonders günstig.
Neues aus der Stahlküche: nicht nur für Autos
Der Stahlanteil einer Autokarosserie liegt bei rund 30 Prozent, je nach Hersteller und Modell. Dabei werden üblicherweise mehr als zehn verschiedene Stahlsorten verarbeitet. Und immer geht es darum, das Gewicht zu reduzieren und dennoch die Sicherheit zu erhöhen.
Das Stahlgewicht kann Klose zufolge auf zwei Wegen verringert werden. Entweder man nutzt besonders feste Bleche, die dann dünner ausfallen können, oder der Stahl selbst wird leichter gemacht. Das geht, indem zum Beispiel leichte Elemente wie Silizium oder Aluminium zulegiert werden. Ein Beispiel ist der von der Salzgitter AG entwickelte hochfeste und hochverformbare HSD®-Stahl.
Die Salzgitter-Forscher arbeiten aber natürlich auch an neuen Stahlsorten für andere Branchen, zum Beispiel für Kraftwerke und Pipelines – oder für Haushaltsgeräte wie Kühlschränke oder Waschmaschinen.
Riesiger Innovationsschub
Gerade in den letzten zwei Jahrzehnten hat die Stahlbranche stark in Forschung und Entwicklung investiert und die technologische Entwicklung beschleunigt. „Es hat einen riesigen Innovationsschub gegeben“, bekräftigt Klose. Das Ergebnis: Es wurden viele neue und stark nachgefragte Stahlsorten entwickelt.
Dabei ist Stahl immer eine Mischung – Fachleute sagen dazu „Legierung“ – aus viel Eisen, ein wenig Kohlenstoff und weiteren chemischen Elementen, zum Beispiel Silizium oder Aluminium. Auch seltenere Stoffe wie etwa Mangan, Chrom oder Titan, Vanadium, Niob oder Molybdän kommen zum Einsatz. Welche Stoffe in welchen Mengen gemischt werden, das bestimmt die Eigenschaft eines Stahls. Aber auch jeder einzelne Schritt der Prozessführung, vor allem die Temperaturführung, beeinflusst die Qualitäten des Materials.
Tüfteln im Labor
Geeignete „Kochrezepte“ zu entwickeln, ist Klose zufolge viel Tüftelarbeit. Im Labor werden immer wieder neue Mischungen in Zwei-Kilo-Tiegel gegossen, dann gewalzt, geglüht und getestet, bis die Legierung mit den gewünschten Eigenschaften gefunden ist. „Heutzutage bauen und charakterisieren wir neue Legierungen oft auch mit Computerunterstützung, gewissermaßen Atom für Atom“, berichtet Klose. Vielfach werden neue Stähle auch auf Kundenwunsch gezielt (weiter-)entwickelt. Dabei arbeitet die SZMF in einem Netzwerk mit Forschungseinrichtungen im In- und Ausland zusammen.
Die Entwicklung einer neuen Legierung kann zwischen drei Monaten und über ein Jahrzehnt dauern. Doch die Mühe zahlt sich aus. „Nur mit ständiger Innovation und neuen Stahlqualitäten können wir uns als Konzern im harten Wettbewerb gegen die internationale Billigkonkurrenz behaupten“, lautet Kloses Fazit.